Buhler AG and dsm-firmenich Volunteers Provide Fortification Training to Milling and Edible Oil Companies in Ethiopia
Fortifying foods that are already commonly consumed is of the most effective ways of tackling the micronutrient deficiencies that affect millions of people on the African continent.
PFS is grateful to four of our Africa-based volunteers from Buhler AG and dsm-firmenich who provided fortification training to members of the Ethiopian Millers Association and Edible Oil Association to support them to meet the National Fortification Standard. This was done in collaboration with the Ethiopia Food and Drug Authority and Standards Agency.
Over the course of three(3) days, Oreofe Odunsi, Rishan Elmneh and Kidist Tadesse, of dsm-firmenich and Biniam Tiezazu, from Buhler AG trained 32 millers and 29 edible oil companies on topics including microdoser installation and calibration, formulation and ratio adjustment of micronutrients to flour/oil and quality control testing and methodologies.
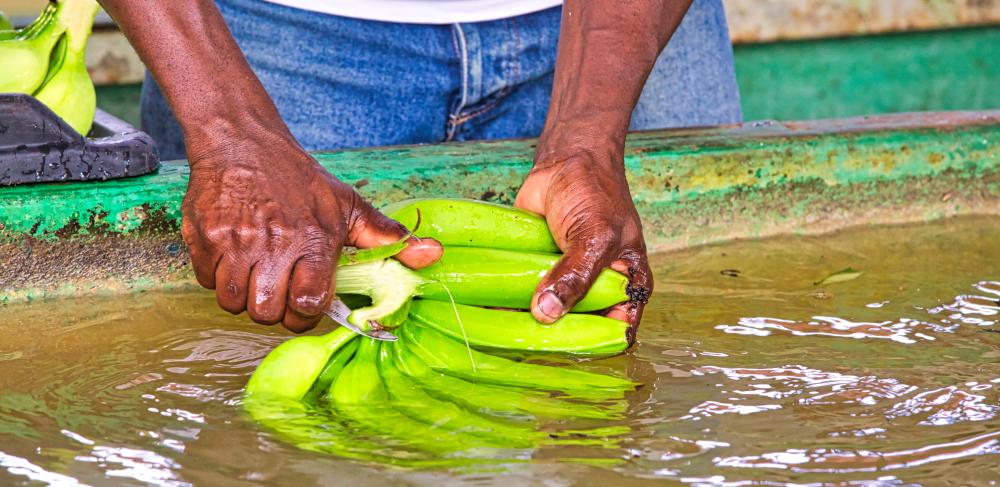
'Small' intervention creates huge impact for Forest Fruit Foods in Uganda
“Eshandy” is the trendiest beverage in Uganda! It’s a refreshing juice made from ripened bananas with no artificial sugars, flavor or color added. It is produced by Forest Fruit Foods (FFF) Ltd, an agro-processing company established in 2003.
Uganda is a leading grower of bananas in Africa. However, most of the produce is either exported or consumed in its natural state. Forest Fruit Foods is one of the few players that processes bananas on a commercial scale, with operations along the entire value chain. They do this because effective commercialization requires greater control on the value chain activities, as banana juice is a highly perishable product.
“Eshandy” is made from a variety of bananas that are native to regions in Uganda and Tanzania. Because of that there are no existing global resources or technical support available for processing these varieties. In addition, when packaged the banana juice does not have a uniform color, with bottles from even the same batch having different shades, which is quite undesirable for consumers. This is why FFF reached out to PFS to learn how they could stabilize their product.
With a background in microbiology and more than two decades of experience in food and beverage manufacturing, J.M Smuckers’ Sarah Mothershead was a perfect fit to help Forest Fruit Foods. Sarah had a number of hypotheses as to what caused the browning but she needed to prove them before she could propose solutions.
“The team, which included talented individuals from Forest Fruit Food Ltd., Partners in Food Solutions, and other volunteer members, was able to work together to understand the banana juice manufacturing and bottling process to develop test plans aimed at reducing the browning that was occurring in the shelf stable banana juice product over the shelf life in a warm environment. We were able to show that using antioxidants at differing points and in varying concentrations within the process serves to effectively minimize browning reactions. We were also able to provide support for the ideas of the FFF interns for further testing protocols and to bolster the food safety attributes of the product.”
Kano Kekurutso of Forest Fruit Foods, said “The team has been excellent with their commitment and level of organization, follow ups and practicality. They have been very realistic and accommodating.”Kano considers that the partnership with PFS is very instrumental, not only with the technical issues, but also the commercial aspects.“Through this project, we have more systematic and clearer technical controls and protocols. What some may consider a ‘small’ intervention will lead to huge results for Forest Fruit Foods. Resolving this browning will increase the shelf life of our product which will in turn increase the volumes of the bananas we purchase from farmers, and will lead to market expansion. We look forward to taking these trials from the lab to commercialization.”
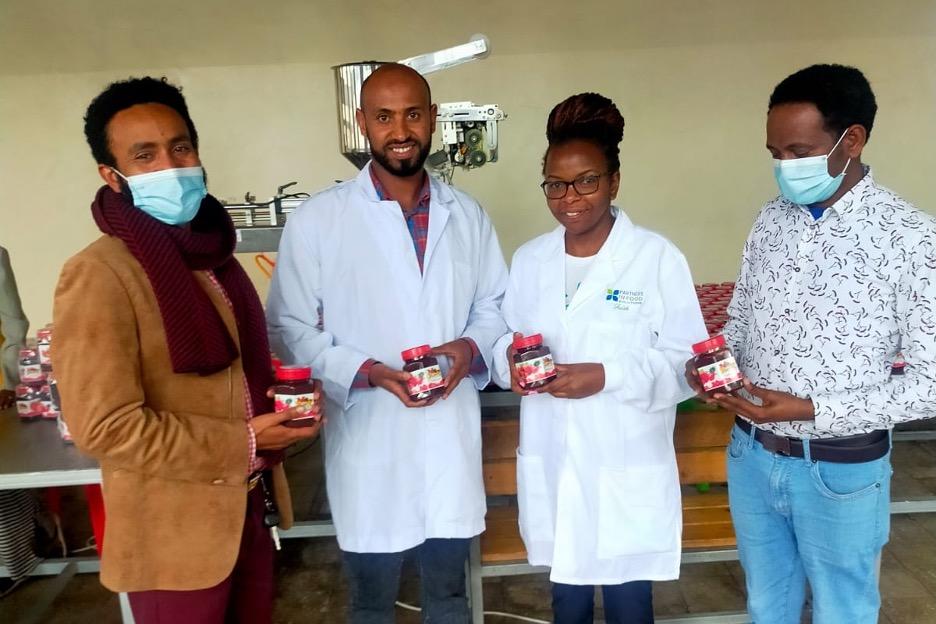
Sales Triple Following PFS Marketing Project for Ethiopian Processor
Living in Zambia as a child, Kenzie Caron had the unique perspective of seeing Partners in Food Solutions (PFS) grow from an idea to the unique and dynamic organization it has now become in the fight against food insecurity. Yes, Kenzie’s father is PFS Co-Founder Jeff Dykstra, who developed the idea for PFS 15 years ago with General Mills. It’s not at all surprising that Kenzie is now a General Mills employee and a PFS volunteer. Her first project supported Cado Industries, a fruit and vegetable processing company in Ethiopia, to develop a marketing strategy for their portfolio of products. Cado Industries was founded in 2017 by Birhane Gebiresilassie, to mainly produce jams from locally grown fruits such as strawberries, mangoes, and papayas. Birhane was interested in diversifying Cado’s product portfolio to include other products such as fruit juices and syrups, candied and canned fruit, tomato paste and ketchup. He reached out to PFS requesting support for a marketing strategy not only for their existing fruit jam, but for their expanded product range.
As a senior brand experience planner at General Mills, Kenzie brings brands to life for consumers in her day to day work. She and a fellow volunteer from the J.M. Smucker Company worked to develop a holistic marketing playbook for Cado. They first started out with a SWOT (strengths, weaknesses, opportunities, threats) analysis, identifying the company’s areas of opportunity and weakness. They also evaluated the company’s target base as well as their competitors. All of this fed into the final strategic plan they laid out for Cado.
Kenzie said working on this project was very fulfilling. She not only had the chance to be connected to people from across the world, but also learned a lot, especially from the senior team member from Smucker with whom she collaborated. It was also an eye opening experience for her, deepening her sense of empathy for entrepreneurs like Birhane, who have overcome tremendous difficulties to succeed. “At the time of the project, Ethiopia was in the middle of a civil war and our client had to deal with the challenge of running a business in a war,” she said. “I learned a lot about compassion and empathy working with him, and my perspective was definitely broadened.”
After implementing the recommendations of the marketing strategy, CADO Industries’ sales tripled in comparison to the previous year. They also digitized their operations, developing an online presence which helped multiply their customer base. Birhane is grateful for the support offered to him. “Kenzie and her fellow volunteers were very helpful, humble and professional. They owned the project from end to end and have helped make my business a success!” For Kenzie, seeing Birhane’s responsiveness and acceptance, and implementation of their recommendations so quickly was very rewarding. It also showed her that as different as their worlds are, universal marketing truths still apply.
Kenzie’s advice to others interested in volunteering? “Just do it! As long as there are a couple of things in the description of the project that interest you and you have familiarity with, the rest will fall into place. You could also be partnered with others who may fill those gaps.”
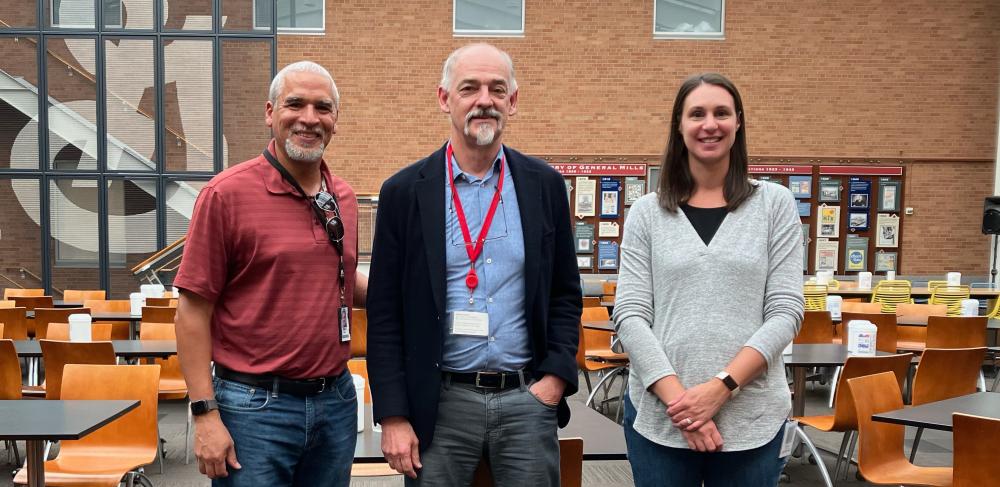
Sweet Connections Cross the Globe
Sweet Connections Cross the Globe
When Chris Majors, a director of quality and regulatory for General Mills, met Daniel Ball, managing director of the Zambian client Forest Fruits, in Zambia during a PFS visit last October, they agreed to meet again. So when Daniel was in Minnesota last month to visit with a honey broker he stopped by to see Chris at the General Mills research facility. General Mills and Forest Fruits have one big thing in common - honey.
One of General Mills' biggest products - Honey Nut Cheerios - uses honey as a key ingredient and Forest Fruits is a processor of honey. A client of PFS since 2019, Forest Fruits is committed to improving rural livelihoods by developing business in rural areas of Zambia. It works with traditional beekeepers living in remote forests near the source of the Zambezi River in north western Zambia through an out-growers system that includes training and extension services. Their major product is honey, Zambezi Gold, that is distributed locally to all major retail supermarkets and grocery stores and is exported to the EU and southern Africa subregion.
Chris connected Daniel with Sarah Schramke, another R&D scientist, to see what possibilities there are. "He (Daniel) would be selling to a broker and then we would be buying from that broker," said Chris. "The brokers will blend honeys too so if we get the right blend with his honey in it, that's the idea." We'd be thrilled if the honey from one of our clients could be part of the great products of PFS' founding partner General Mills, bringing something very sweet full circle.
Photo left to right: Chris Majors, Daniel Ball, Sarah Schramke.
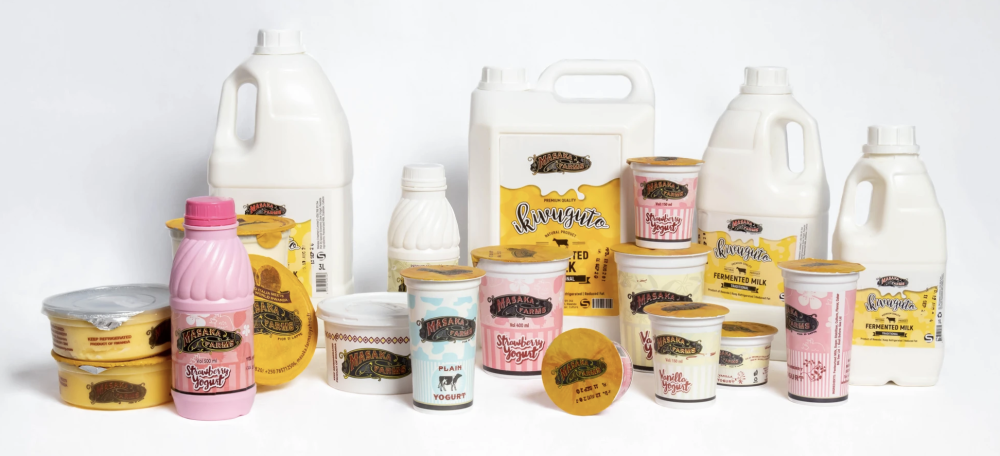
Dairy Brand with a Social Mission is Number One Yogurt Brand in Rwanda
Masaka Dairy has a unique competitive advantage that many in Rwanda would consider a liability - over fifty percent of their staff are deaf.
Luke Lundberg, the current CEO of Masaka, says that his staff has a particularly well-developed attention to detail because of their hearing impairment. “When you lose a sense it often heightens your other senses,” he said. “Our deaf staff have a lot of ownership and pay incredible attention to detail. They want to make sure every product we send out is as perfect as possible.”
From its inception in 2015, Masaka Creamery recognized that offering employment to deaf people was a better way to address their needs than charity. The company has grown steadily and in addition to employment, also provides training for the deaf community; something that is not widely available in Rwanda.
Sandy Efaw, contract manufacturing manager at J.M Smucker found her first volunteering project with PFS so rewarding that when the opportunity came for her to volunteer on another project, she took it up with little hesitation.
Sandy was part of a team of volunteers that supported Masaka in attaining certifications from the Rwanda Food and Drugs Authority (RFDA) which allows them to increase brand trust and eventually export their products. In addition to yogurt, they also produce fermented milk, cream, butter, and other dairy products with an average daily production of 4,000 liters.
To receive HACCP certification, they needed to develop a Site Master File (SMF), which is an internationally recognized record with specific information about their manufacturing operations. Sandy and the team of volunteers worked directly with the Masaka staff to put this document together.
Sandy was familiar with a Site Master File through her work with external contractors at Smucker, but it was not an area she was directly responsible for in her job. She set off to research as much as she could to try to learn and understand the scope of the task.
The terrain was just as unfamiliar to her co-volunteers, so they all dug in together to learn in order to offer Masaka the best results. That collaboration made the difference. They even worked together outside of project hours because of the importance of the project.
The Masaka team’s responsiveness and receptiveness to the different proposals from the volunteers made the extra time and effort worth it. Masaka now has their SMF in place and they are awaiting certification from the Rwanda FDA.
“I benefited a lot from working on this project and working with the other volunteers. It has actually been helpful for me in my job as I now have a more in-depth perspective on what to look out for and expect from our external contractors I work with,” she said. “The uncertainty at the beginning of the project worked out for the best at the end, proving that sometimes you get better results if you don’t have your mind dead set on the end goal.”
Sandy is on a roll when it comes to successful PFS projects and is looking for her next opportunity. She says that everyone at Smucker can have the same positive experience that she’s had. “I’d encourage my colleagues to volunteer even if they are not sure of exactly what they’re doing when they jump in. It’s definitely enriching and volunteers end up getting more out of it than they realize.”
Luke affirms this saying, “Masaka has always had a baseline, but working with PFS has really elevated a lot of our processes, documentation and certifications, which we really appreciate. The volunteers have been very helpful, gracious and understanding, even when we don’t hit all the deadlines. It has been a great opportunity for the Masaka team to learn how they can improve things and it’s something that we really enjoy about this partnership.”