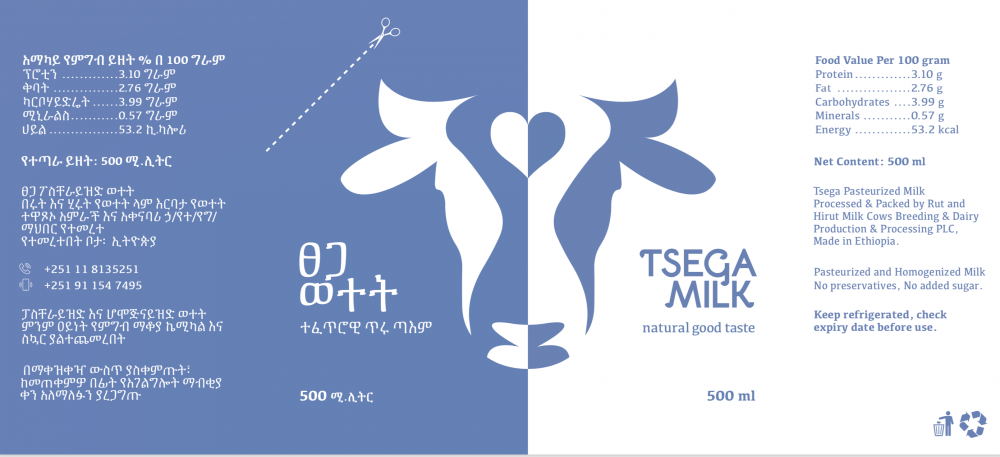
Supporting Dairy Farmers in Ethiopia Through Impactful Designs
Kris Zamora is an in-house creative at Hershey and spends his days supporting internal teams by developing content from animated advertisements to conceptualizing new product ideas. Motivated by his desire to make a greater impact, Kris joined a brand design project with Alliance for Inclusive and Nutritious Food Processing (AINFP) client Rut & Hirut that allowed him to learn new skills and give back in a meaningful way. Rut & Hirut is a women-owned dairy processing company located outside Addis Ababa that produces various products including pasteurized milk, yogurt, cheese and butter. The company was established with the goal of improving the livelihoods of farmers, and has supported hundreds of female dairy farmers over the years. “All the work that was done with this volunteer project not only benefits the business owners, but also the broader community,” Kris said. “Knowing my work made a difference for someone else’s life directly is all that I could ever ask for.”
In collaboration with PFS, TechnoServe and USAID, Kris worked on creating an effective design strategy that would allow Rut & Hirut to penetrate the bottom of the pyramid market and increase sales. “I can’t speak Amharic (the official language of Ethiopia) nor can I read or write it,” said Kris. “Working on the packaging design for this project did require a little bit of patience on my end given there was a quick learning curve.” This project not only pushed Kris outside his comfort zone, but allowed him to build upon his communication and cross-cultural competencies. “When I was working on the logo rebrand, part of the logo had a small heart shape icon in it. I had to ask myself ‘Is a heart shape universally recognizable? Does a heart shape mean something different in other cultures?’ This is something I normally do not need to consider in my day job and is something that I believe will make me a better overall designer and creative.”
Kris’ favorite part of the project was during the packaging design concept phase for Rut & Hirut’s milk products. Initially, Rut & Hirut chose the design concept that most closely reflected their current brand look. Before making any final decisions, Rut & Hirut decided to go out into the community and share the design concepts with the locals to see which designs they liked the most. “I thought this was a smart and strategic decision by Rut & Hirut to get the local community’s input on the design,” said Kris. “Ultimately, after receiving feedback from locals, Rut & Hirut decided to go with the bolder packaging design concept. This look was more aligned with what their current and future consumers wanted and brought some valuable insights into our packaging design project.” Since the project closed last year, the product in its new packaging design has entered the market. Rut & Hirut have reported that consumers are finding the improved packaging to be very attractive.
*The Alliance for Inclusive and Nutritious Food Processing (AINFP) is helping unlock the potential of the food processing sector by providing technical assistance and sector-wide training to food processors in Ethiopia, Kenya, Tanzania, and Zambia. AINFP is co-funded by the U.S. Agency for International Development and by Partners in Food Solutions, through private funding and in-kind contributions of employee time from its corporate partners. TechnoServe is leading project implementation on the ground.
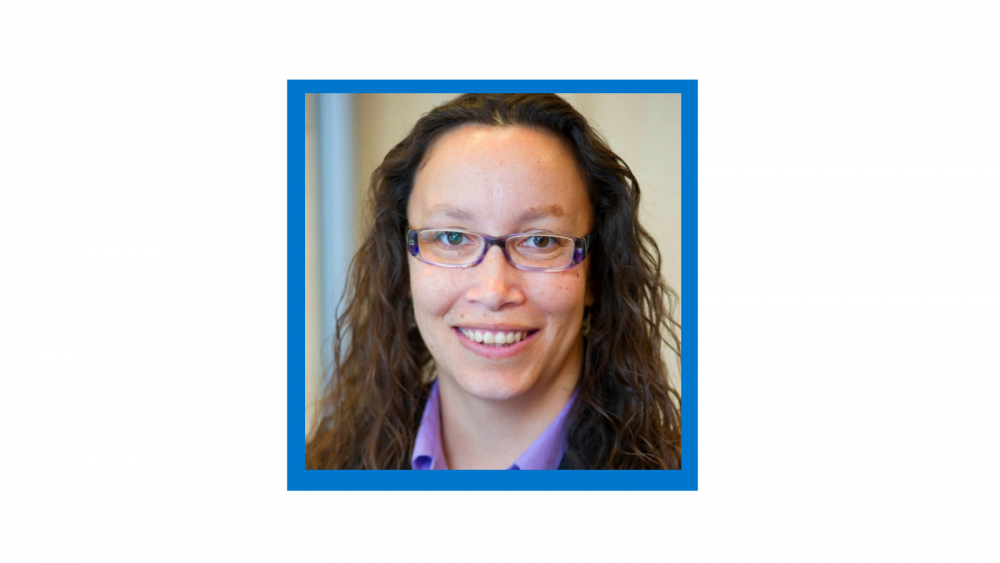
Sharing in the Client's Journey
Carol Jeffrey-Smith has been a volunteer with PFS since 2016 and has been involved in six volunteer activities. She also serves as a PFS champion and is a valuable part of the Hershey-PFS partnership.
PFS: Please tell us more about yourself.
CJS: I have worked in Information Services at Hershey for nine years in both Canada & the US. I have been a long-time volunteer at PFS, mostly as a Client Lead. I enjoy bringing together volunteers and clients to complete specific projects. I have been very fortunate to work with five different clients in this role. I have learned so much from all the fantastic people involved in PFS projects and it has been an amazing experience!
PFS: What is your main motivation for volunteering with PFS?
CJS: My main motivation for volunteering with PFS is the opportunity to meet new people, learn from other volunteers and watch the clients grow through this experience.
PFS: You’ve taken on several Client Lead roles throughout the years, what’s your favorite part about being a Client Lead?
CJS: The client’s energy and dedication to growing their business while managing a busy operation. It is a real privilege to share in the client’s journey. I am currently the Client Lead for Assisi Foods in Ghana and their leaders have demonstrated terrific focus and initiative in achieving key goals. They have a clear vision for Assisi Foods and I am delighted at the opportunity to make a small contribution towards their continued success.
PFS: How does it make you feel knowing Hershey has this volunteer opportunity for its employees?
CJS: Proud. As a company, Hershey is committed to supporting volunteer initiatives that create real value and have a tangible impact. I am very happy to be part of an organization that “walks the walk and talks the talk.”
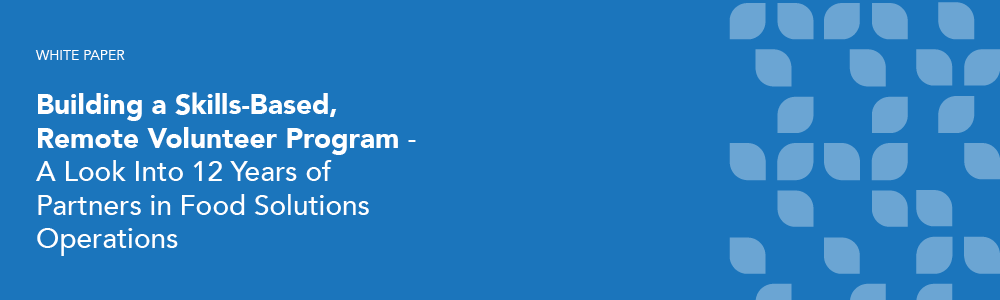
White Paper: Building a Skills-Based, Remote Volunteer Program
Partners in Food Solutions releases a new white paper documenting how we built our virtual, skills-based volunteering program. Through twelve years of innovation and growth, we have honed our program to bring maximum impact for both our African food company clients and volunteer experts. Read our report to find out more.
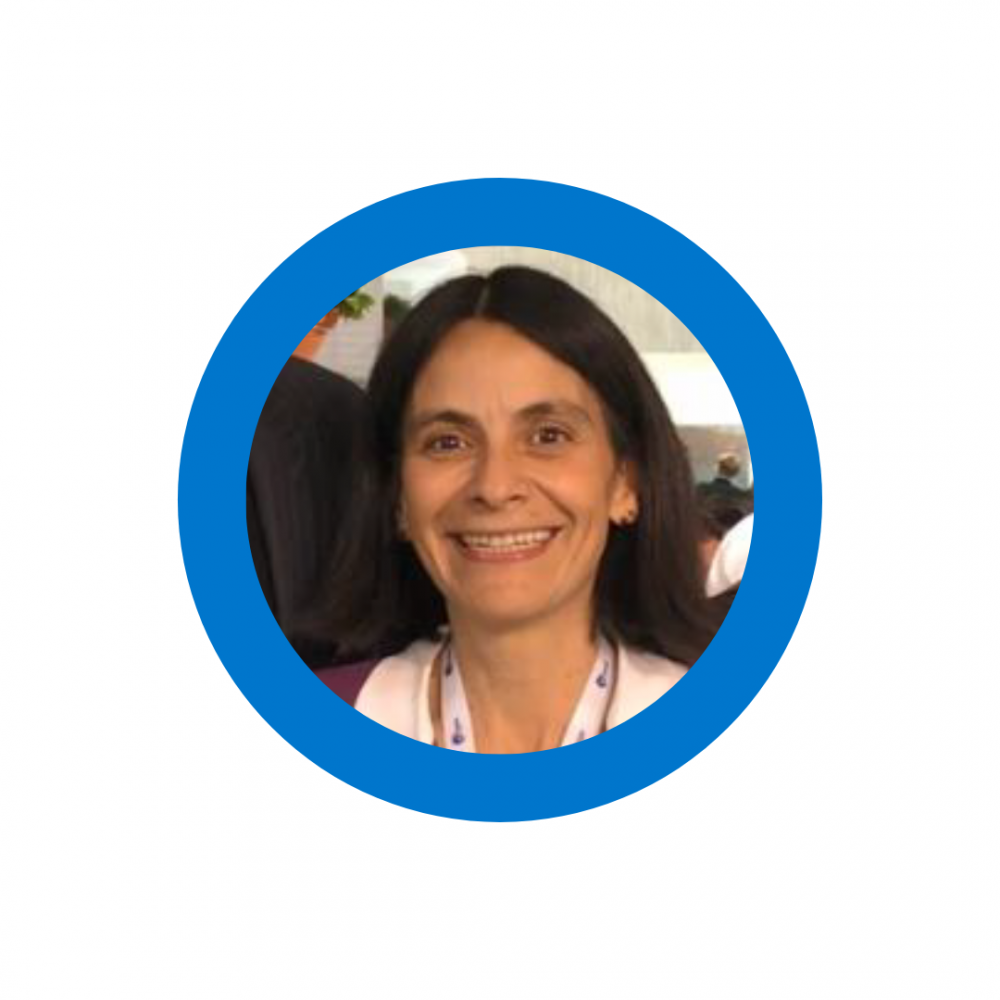
Q+A with DSM Regional Key Account Manager Adriana Molina-Hoeppner
PFS: Please share more about yourself.
AH: I studied food engineering and have worked in sales for various food ingredients throughout my career. I enjoy working in multicultural teams and have spent the past several years volunteering with PFS as a Client Lead for a couple of different clients.
PFS: Why did you get involved with PFS?
AH: I joined PFS because I wanted to help and give back a little of what I receive every day.
PFS: How does volunteering with PFS help DSM employees live out their purpose?
AH: I believe volunteering with PFS is a good way for DSM employees to ‘Do Something Meaningful.’ Volunteering is about a one hour a week commitment and you get to use your skills and knowledge to help better the lives of others.
PFS: What is the most interesting thing you’ve learned while volunteering with PFS?
AH: You can have a great impact and help others with little time investment.
PFS: If someone is interested in volunteering but may be hesitant to start, what would you say to them?
AH: Just try it! Once you try it for yourself you will see how great the opportunity truly is.
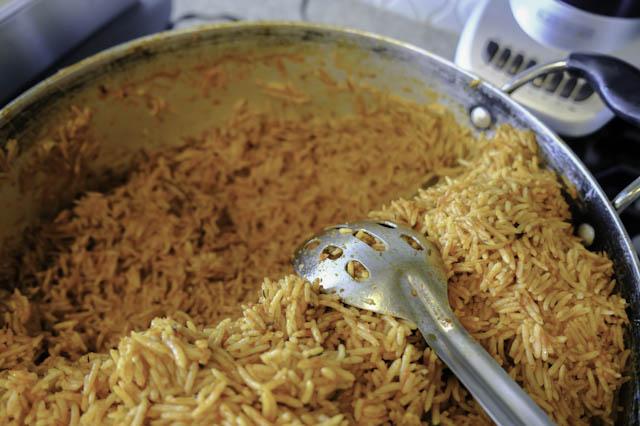
Being Part of Something Bigger Than Yourself
The national dish of Nigeria, Jollof Rice, is a spicy staple food served around the country and gets its signature bright red color from tomatoes. The country is now the second largest producer of fresh tomatoes in Africa. Yet despite that, it is also one of the world’s largest importers of tomato paste. In an effort to strengthen domestic markets for tomato growers, Tomato Jos, a tomato farm based in northern Nigeria, wanted to expand their operations and start making their own tomato paste. Given that this was uncharted territory for the company and their team, they looked to Partners in Food Solutions (PFS) for support in the areas of warehouse space design, staffing, process optimization, and packaging design.
DSM’s Florian Jardin took on the project manager “Client Lead” role for all of these projects with Tomato Jos. “I was drawn to helping them because of the social impact I could directly have,” said Florian. “I want to use my strengths to support start-ups with a great purpose and PFS let me do that with Tomato Jos this past year.” Florian, a global category manager at DSM, used his skills and expertise to not only make sure projects moved along in a timely manner, he also shared business and distribution strategy recommendations with the client CEO. “Initially I was a bit afraid to fail and let the client down, but after the first call I had a great feeling because I knew the volunteer team and I could bring real value to the client and help them reach their goals.”
Within weeks the volunteer project team was able to develop an efficient warehouse design plan that addressed gaps in Tomato Jos’ storage systems, which could now lead to significant cost savings. Volunteers were also able to recreate packaging design files that suited the client’s needs.
“Our experience working with PFS has been very positive,” said Francis Bulus, processing project manager for Tomato Jos. “Considering the fact that our core business objectives for the year revolve around setting up the factory and running it efficiently, the ongoing support from the PFS team, which has helped push a lot of that forward, has been invaluable. It’s to the point that it’s had a ripple effect on the company as a whole because a lot of the decisions constructed by the support from the team translated into smart business decisions across other business units.”