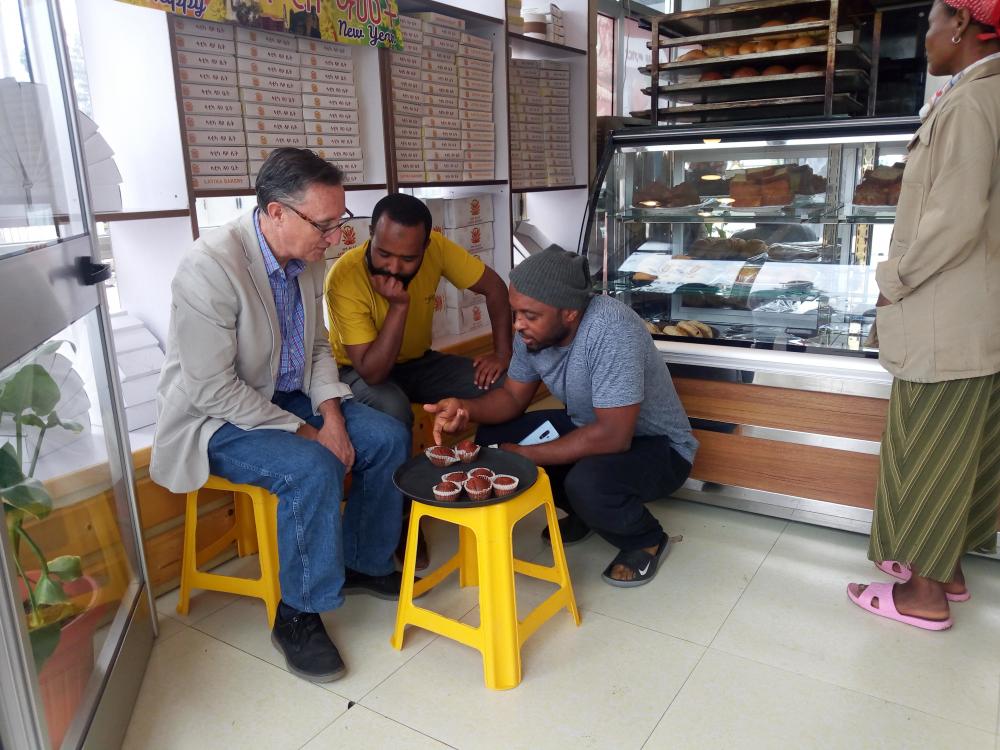
A Recipe for Improving Nutrition
Sometimes it takes a virtual village to make a delicious and nutritious loaf of bread. DH Geda Flour Factory, a wheat processing company in Ethiopia, was interested in seeing if they could create a nutritious product using the leftover wheat germ from their flour processing. They looked to Partners in Food Solutions (PFS) and TechnoServe, with the support of USAID, for assistance.
Incorporating wheat germ into products like bread and muffins adds vital nutrients such as fat and fiber, and improves the overall nutritional value of the product. DH Geda, along with its customer Latika Bakery, worked with PFS volunteers and TechnoServe staff on a product formulation project that utilizes the leftover wheat germ from their milling process.
A critical element of the project was creating a baked product that was acceptable to local tastes. To develop it, volunteers tested varying levels of wheat germ in bread and muffin formulations. They also had local customers of the bakery try different recipes to see which one consumers would prefer. After many rounds of baking and dozens of taste tests, the team provided DH Geda with a bread recipe that included flour and wheat germ. They can now use it as a product example to show their commercial customers that adding nutritious wheat germ can produce delicious products.
DH Geda has already seen success and several bakeries have wheat-germ enhanced products in the market. There is also great potential that even more will be included in future products because the team is working with the Ethiopia Millers Association to encourage more Ethiopian millers to produce wheat germ and sell it.
According to Yohannes Tesfu, a senior food processing specialist with TechnoServe, “The wheat germ product was not widely known in the market... DH Geda is the first company in the country to sell wheat germ and they have so far sold 200 kg (more than 400 lbs) in the first couple of months since the project was completed.”
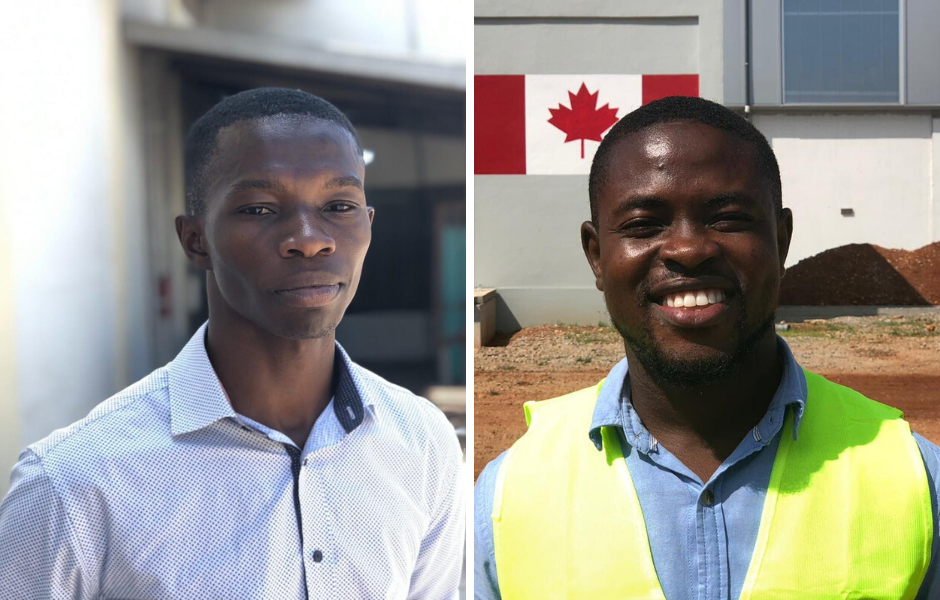
The Power of Apprenticeships
Before being hired by Premium Foods as their quality assurance officer, Jacob Sarfo served as an apprentice with Premium Foods through the Partners in Food Solutions (PFS) apprenticeship program. “After graduating from Kwame Nkrumah University in Kumasi, Ghana, I knew I wanted to work in food production. When I learned that PFS can make that come true through their apprenticeship program, I gladly applied,” said Jacob. Once the one-year apprenticeship ended, Jacob was hired by Premium Foods where he utilizes the skills he learned from his apprenticeship. “I use a lot of the skills I learned from the food safety apprenticeship program including running quality checks, liaising with external food safety auditors and building the self-confidence I need to excel in my job.” In the next five years, Jacob would like to own a business but ultimately wants to help others realize their potential just as he did through Partners in Food Solutions.
Premium Food’s current apprentice, Maxwell Bruce, is also in the Partners in Food Solutions apprenticeship program and shares similar goals to Jacob. “I knew joining the PFS apprenticeship program would give me the exposure to the industrial food system that I desired and that’s why I applied,” he said. Maxwell has the unique opportunity to work alongside former Premium Foods apprentice, Jacob, and learn about food safety from someone he can look up to. “Working with Jacob motivates me to work harder. He helps me move outside of my comfort zone and shows me how to apply the knowledge I learned in school to real-world scenarios at Premium Foods.” Once finished with his apprenticeship at PFS, Maxwell would like to go back to school to obtain his Ph.D. in food science and technology, and hopes to work for an organization that addresses food security.
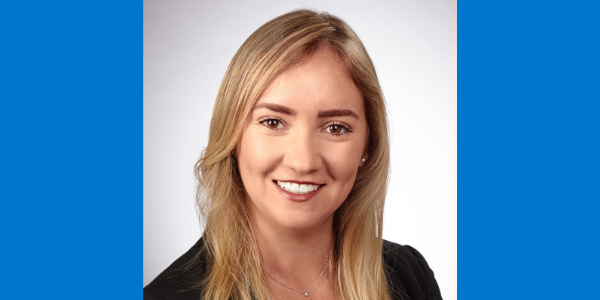
Improving Food Safety Through Global Partnerships
“I come from a developing country and I know how hard it can be for small businesses to get resources and support. I thought PFS was a great opportunity to give back and share some of the knowledge and skills that I’ve acquired over the years,” said Regina Barcena, senior manager of food safety & quality at The Hershey Company. Regina is currently volunteering with Partners in Food Solutions on a HACCP implementation project in Ghana.
PFS: Please tell us a little about your background.
RB: I am originally from Mexico and first started at Hershey as an intern there. I moved to our corporate office in Pennsylvania ten years ago and have had a few different positions including quality specialist, sanitation supervisor and quality engineer. I am currently the senior manager of food safety & quality at our Stuart Draft Plant.
PFS: Why did you decide to get involved with Partners in Food Solutions?
RB: I come from a developing country and I know how hard it can be for small businesses to get resources and support. I thought PFS was a great opportunity to give back and share some of the knowledge and skills that I’ve acquired over the years.
PFS: What has been the most rewarding thing about being a PFS volunteer for you?
RB: In general, the fact that I am able to improve the food safety culture of a developing country is very rewarding. Every year, there are millions of cases of foodborne illnesses, especially in low and middle-income countries. As a PFS volunteer, I delivered a good manufacturing practices training through video and demonstrated things like record-keeping and good hygiene practices to a client. I feel the work done by myself and the rest of the volunteers is raising food safety awareness and we’ve been able to reduce cases of foodborne illnesses.
PFS: Tell me more about the HACCP project you’re currently working on?
RB: The primary objective of the project is to develop a HACCP plan that will lead to an International Quality Certification. Gaining the additional certification will allow them to sell products in other countries and therefore increase their profits. It has been a very rewarding experience to work with volunteers from other companies like General Mills and Cargill. When we get together to help our client we are one team of experts, creating value for the final consumer. I consider this a perfect opportunity to be able to share my knowledge, learn from other experts and help people from other cultures and countries. Our next step is to train their 34 employees through a conference call and I am really excited to be part of this transformation.
PFS: What skills have you used/developed as a PFS volunteer?
RB: I’ve learned to be a partner. When I first joined PFS, I thought we were going to take on more of a consultant role. But, after the first meeting, I realized that I was going to learn just as much from them as they were from me. Volunteering with PFS and supporting African companies helped me realize that you can make big changes with small programs. I’ve been able to implement some of those learnings in my day job, and the learning and results have been fantastic.
PFS: How does the fact that Hershey supports PFS make you feel?
RB: Making moments of goodness is in Hershey’s DNA. I am grateful to work for a company that supports programs like PFS and allows me to develop my career in a global environment while at the same time supporting those in need.
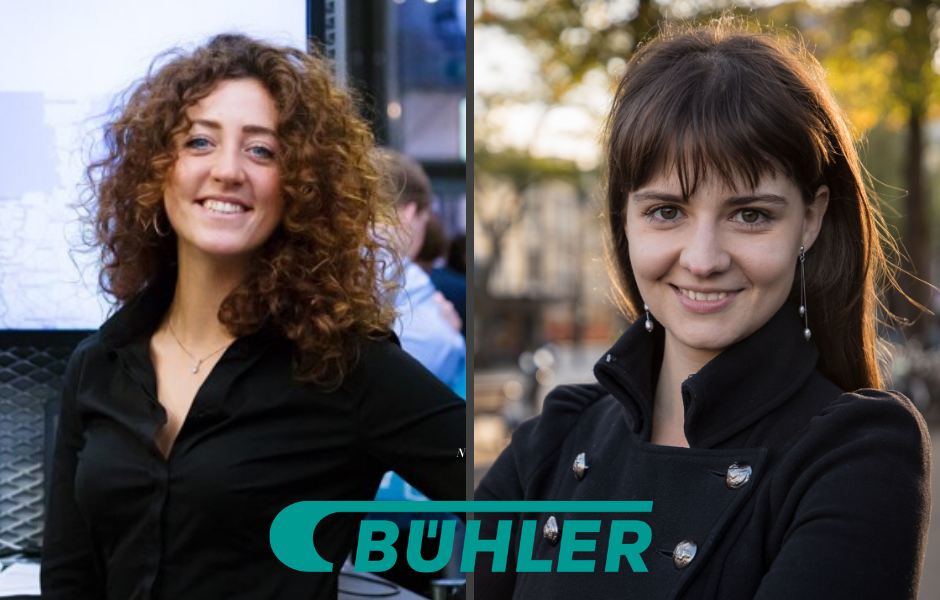
Two Bühler Volunteers Share Their Experience as Client Leads in 2019
We connected with first-time PFS volunteers, Camilla Cavalier and Sorana Ionita, to learn more about their recent experiences as client leads. When asked what she would say to someone who’s interested in joining PFS, Sorana, a Supply Chain Project Manager at Bühler, said, “If a certain project or company sparks your interest, either because you relate to their business or you have some of the skills required for the specific position, you should go for it! Even if the position doesn’t align with your day job’s description I would suggest you take a chance, volunteer as a client lead and enjoy the ride.”
PFS: Why did you decide to get involved with PFS?
CC: It didn’t take much for me to join. PFS aligns with my personal and professional interests, and since Bühler is an active partner I had some colleagues who were already involved. When I was asked to join a project I knew I wanted to get involved right away.
SI: I attended a training about cocoa farming in Ghana in early 2019 and that experience really opened my eyes to food production in Africa. After the training ended I knew I wanted to get involved in improving food security in Africa, but didn’t know how I could directly contribute as an individual. At the same time, a colleague introduced me to PFS and it was like the stars aligned – this was my chance to get involved with Africa’s food system.
PFS: Why did you choose to be a client lead for the company you work with?
CC: The client lead position for Valid Nutrition really aligned with my job at Bühler. I’m a project manager and already had experience working with remote and global teams so it seemed like a good fit for me. However, I didn’t have any experience in the project topic I was managing, which was a good challenge for me. I was exposed to quality lab design work that I would have otherwise never been exposed to in my day job at Bühler.
SI: My client, Fastizers Foods and Confectionery, was working on a food safety and quality control project, and a snack product development project involving cookies and biscuits. At Bühler, I am a supply chain project manager and do not work with food safety or product development. However, I am familiar with biscuit, cookie and waffle processing machinery, which helped me contribute in some areas of the projects with the client.
PFS: What’s your favorite part of being a client lead?
CC: I love coordinating the meetings and making sure everyone is getting value out of it. Sometimes it can be challenging to schedule calls with people from across the globe, but once we got the preliminary logistics worked out we were able to have fruitful discussions and I could keep the project moving forward through recap notes, delegating tasks, etc.
SI: I have really enjoyed working with people from such different backgrounds and cultures other than mine. I’ve been introduced to different perspectives and experiences that I may not otherwise get to interact with day-to-day. I’m always looking forward to my next status call!
PFS: What would you tell someone who is interested in becoming a PFS volunteer, but is hesitant to join?
CC: I would let them know that whoever joins as a volunteer is well supported by the PFS team. They’re available to answer your questions at any time and will be there to help you keep the project moving forward.
SI: If a certain project or company sparks your interest, either because you relate to their business or you have some of the skills required for the specific position, you should go for it! Even if the position doesn’t align with your day job description, I would suggest you take a chance, volunteer as a client lead and enjoy the ride.