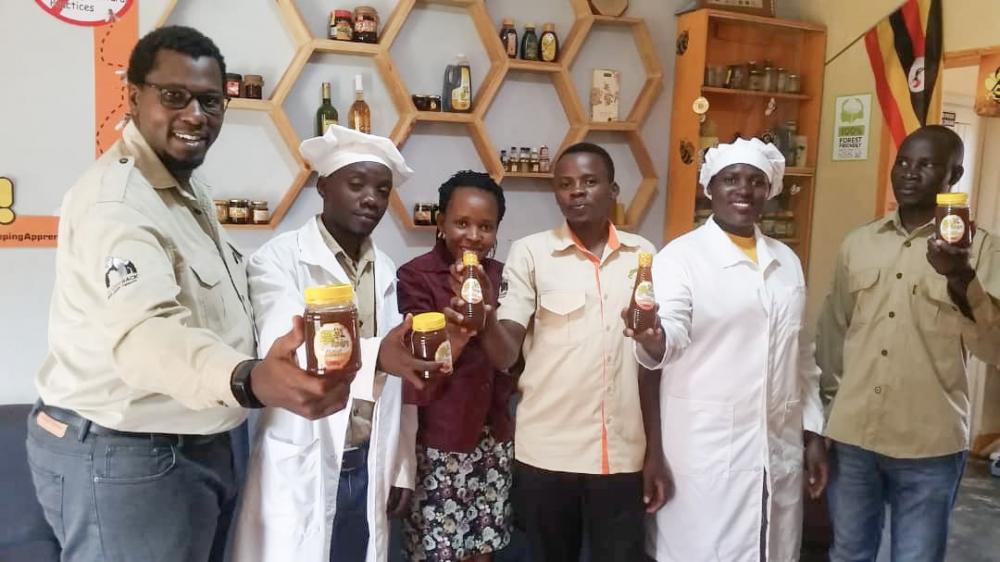
General Mills in Europe decided to try something different when forming a volunteer team to work with Golden Bees, an Ugandan company that produces honey, beeswax, and propolis (bee glue). The team was only comprised of General Mills employees based in Europe. And while there are many benefits to working on a cross-company, geographically diverse team that is the usual makeup of a PFS volunteer team, the Golden Bees volunteer team discovered many benefits to collaborating on a project together.
One of the first people to join the team was Carlota Gonzalo, an experienced PFS volunteer and quality ingredients manager based in Spain who specializes in commodities such as honey, cereals and edible oils. “The Golden Bees project was unlike any previous PFS project I had been involved with,” Carlota said. “Having a team of volunteers from General Mills - Europe allowed us to expedite the project onboarding phase and start work really quickly. Typically it takes some time to learn about the other corporate partners and their work styles, but we already understood one another. Plus, scheduling meetings was a lot easier since we were all on the same continent and not dealing with different time zones,” she continued.
Within the Golden Bees project, there were two very different parts - designing a quality management system and mini quality control lab, and creating a computerized accounting system. Carlota focused on the quality management and lab, while other colleagues focused on the accounting system. Carlota, although familiar with quality management systems due to her background, was not familiar with the lab portion. “I love working globally and learning new things so I wasn’t afraid to get involved in a project where there was a portion I was unfamiliar with,” Carlota said. "I gained a lot from the Golden Bees project because I made new connections in the General Mills R&D and lab departments that I had not previously made, as well as gained a better understanding of what goes on during honey lab testing. I now use that new knowledge in my day job when I am communicating with honey suppliers. I’m able to do my own job better and also get to build a deeper relationship with my clients, who really appreciate the honey lab experience I’ve gained.”
After the project ended, Carlota and her team received great feedback and heartfelt thanks from Golden Bees Founder Brian Mugisha. “We are grateful for the immense contribution you have extended to us. And to the entire PFS and General Mills staff, you are such a wonderful group of people and there is no way we can pay you back other than working towards improving Golden Bees to one day be a General Mills of Uganda!”
Because of the General Mills Europe team’s recommendations, Golden Bees has enhanced their lab and increased the quality team’s capabilities. They are also using an inventory management tool built by General Mills volunteers. It’s a significant contribution to a company that supports 2200 local beekeepers annually and Carlota and the team went on to win the Global Volunteer Award, presented by the General Mills Foundation, for their involvement with PFS and the Golden Bees project.
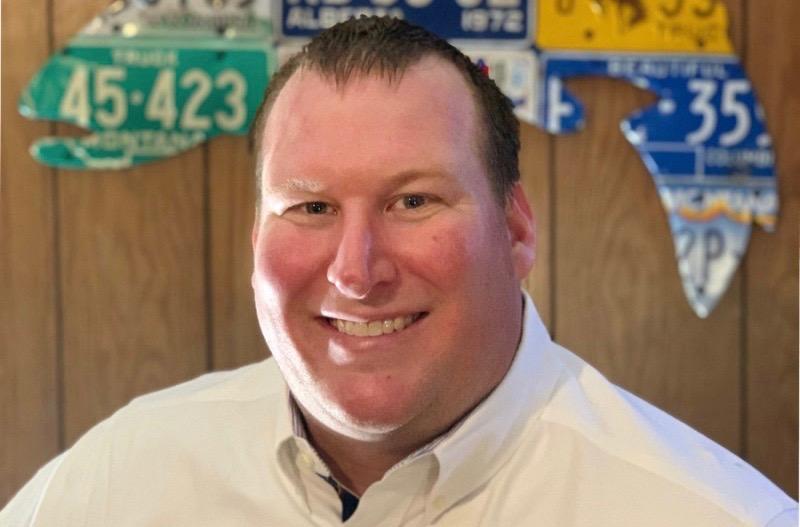
When asked what the most interesting thing he’s learned from being a PFS volunteer, Mark Molamphy quickly responded, “Although PFS is a remote volunteer model and there are challenges with not actually being on the ground, we’ve been able to provide real solutions to real problems for each project I’ve volunteered on. It might not seem like much but volunteering a couple hours a week can actually make a world of a difference for a PFS client.”
Mark Molamphy, a facility manager at Cargill's Indianapolis maize milling facility and an entrepreneur with his own start-up milling business said, “Through PFS we’re using an entrepreneurial mentality to find solutions, and we’re practicing adaptability and flexibility while implementing them.” On one project, Molamphy and a volunteer team from DSM and Cargill established a fortification unit for Lina Millers, a women-owned maize processor in Tanzania. Molamphy and his team needed to source and install a piece of microdosing equipment that was compatible with the existing equipment and plant layout. “Not being able to actually see the plant and experience the flow made developing a recommendation more difficult, but we were up for the challenge,” he said.
During the beginning stages, the client shared pictures of the current set up and included a graphic that helped explain when and how the equipment was utilized. Multiple discussions regarding how the maize flour was mixed and blended followed, and a solution concept started being built out. “By utilizing the volunteers variety of backgrounds and varying plant experiences, we were able to recommend and help source a piece of equipment that would work for the client,” Molamphy said. “If we were to do this type of project at our companies, it would have been a relatively simple request. But, because we were working with an emerging food company, we had to think outside the box to research, source and deliver a piece of equipment that fit their specific needs and budget.”
Lina Millers recently received the microdosing equipment that Molamphy and his team recommended and are working with a Bühler engineer to help install the equipment this year. Once the microdosing equipment is fully installed, Lina Millers will be able to fortify all three of their flour blends, comply with food regulations and expand their distribution footprint. Maize is the most widely consumed grain in Tanzania and now that Lina Millers has the capability to fortify their products with additional nutrients, they will be able to supply more nutritious products to a larger percentage of the population.
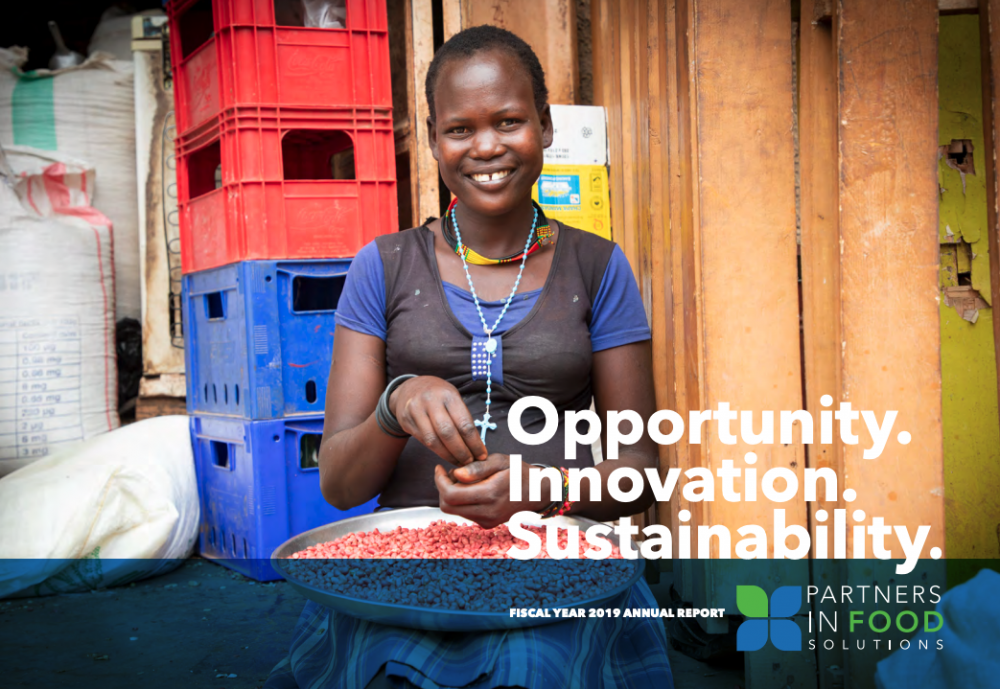
Opportunity is the foundation of Partners in Food Solutions, but it is innovation that drives us and sustainability that inspires us. Read about the amazing African entrepreneurs and volunteers that make our work possible in our new Fiscal Year 2019 Annual Report.
READ THE REPORT
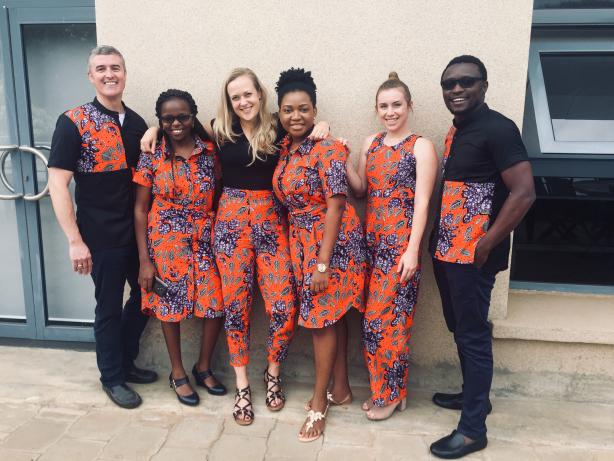
PFS is excited to welcome Faith Ngila and Chenge Wandabwa to our team as Field Program Associates based in Nairobi. They will be working to support volunteers and clients with operations in Kenya, Tanzania, Ethiopia and Uganda.
Faith has a rich background in international development, most recently with Kenya Community Development Fund. She is a published author and is currently working on her masters degree. Chenge spent the past five years working for One Acre Fund, a highly-regarded organization supporting smallholder farmers in East Africa. He previously worked with the Kenya Red Cross and is also currently working on his masters degree.
PFS staff from headquarters, David Dayhoff, Amanda Traaseth and Magdalene Mbaga, along with Yvonne Akorfa Hormenoo, Field Program Associate in Ghana, gathered in Nairobi for intensive training in August. As a fun aside, they discussed getting a PFS "uniform" for the team. With a tradition of colorful fabrics and quick-turn around hand-stitched clothing common across Africa, the team had their "uniforms" ready to wear in three days!